ENVIRONMENT

PT TJB Power Services, situated at Tanjung Jati B Power Station, Desa Tubanan, Kecamatan Kembang, Kabupaten Jepara, Central Java commits to preserve and protect surronding environment in its operation with a view to maintain environmentally sustinable operation.
In order to fulfil the policy :
- Promote a culture of continuous improvement of its management system and pollution in the operation and maintenance of plant and equipment.
- Develop and establish principles and procedures to ensure continuous improvement.
- Comply with all related statutory regulations and other requirements that are in force or may come in to force from time to time.
- Identify, evaluate & control environmental hazards.
- Monitor & audit regularly on going operations to ensure compliance with the procedures.
- Identify, evaluate & record non compliances and take corrective action & regularly verify & review.
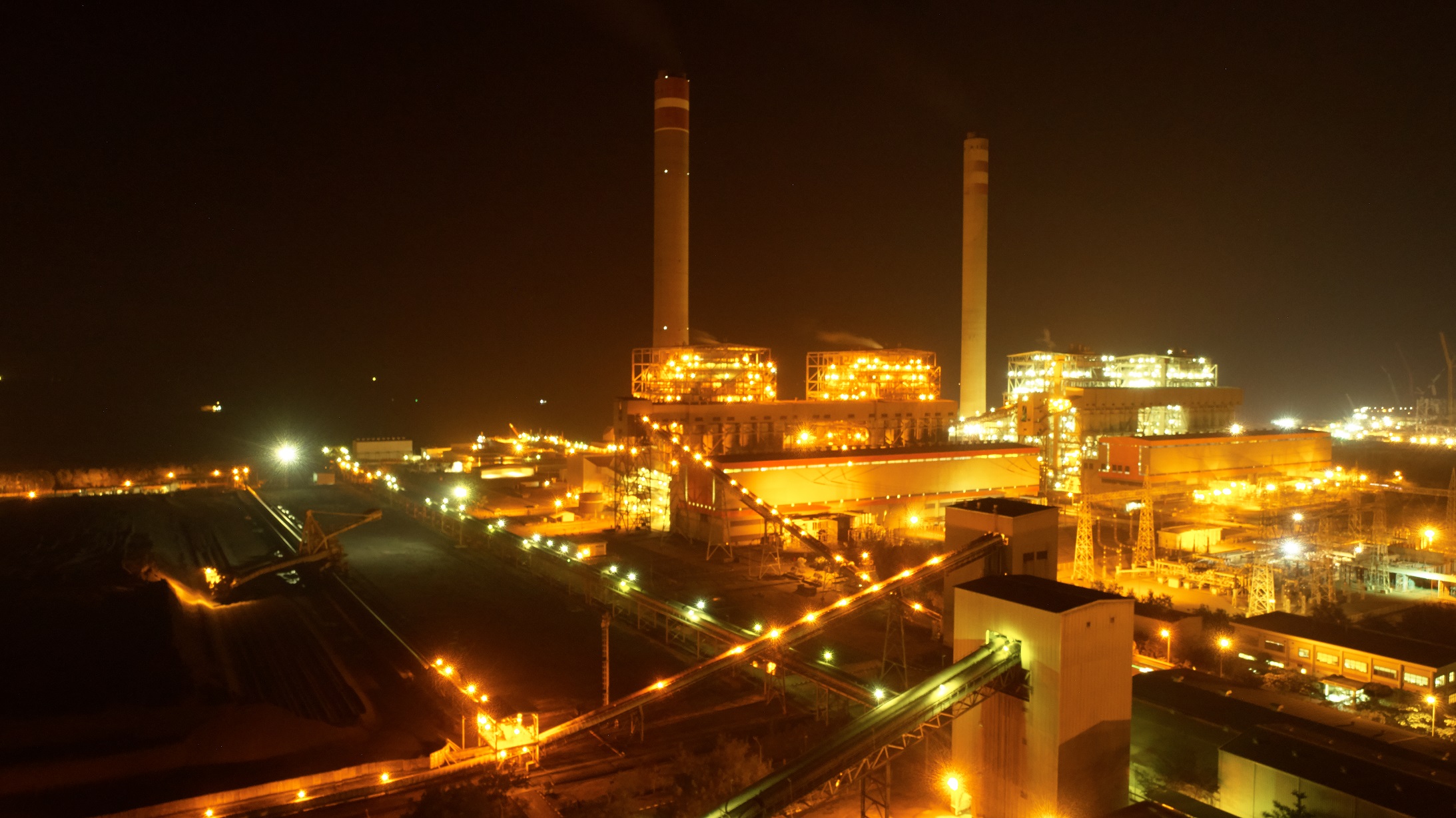
To minimize the environmental effect which caused by coal fired process and provide environmental friendly industry. Tanjung Jati B Power Plant have several facilities such as :
Coal fired power plant installed in Indonesia are fitted with electrostatic precipitators in orderto remove the dust/particulates from the exhaust gas as a consequence of the coal combustion process. At Tanjung Jati B Power Station, the electrostatic precipitators are designed, sized and operated in accordance with exhaust gas flow and draft losses (determined principally by size of the Units).
The electrostatic precipitators are capable of removing 99% og the dust from the exhaust gas. The fine dry dust is transported from the electrostatic Precipitator hoppers by air to the two common Fly ash Silos, from where it is collected to be utilized in the cement industry.
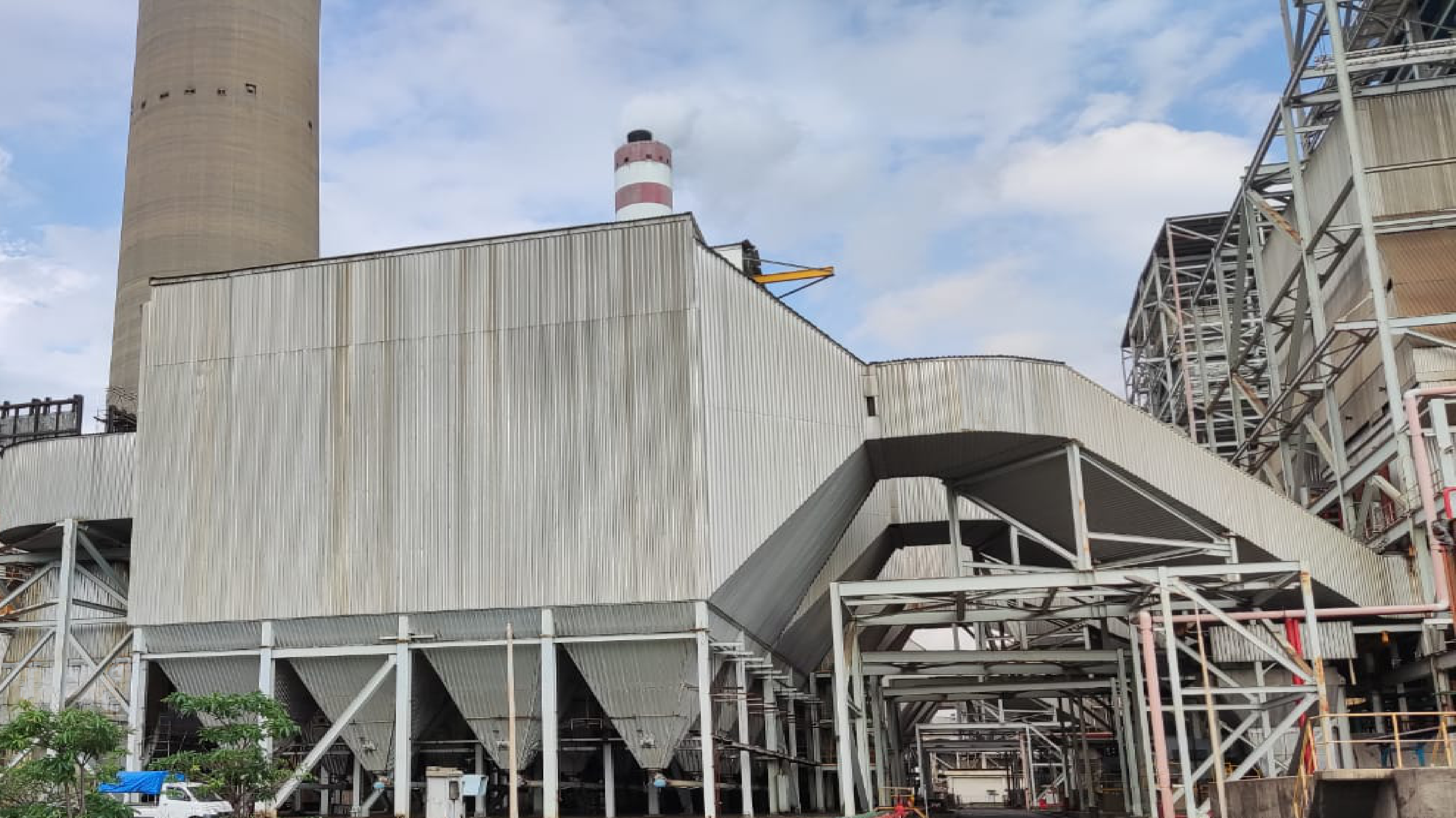
Historically Gaseus Sulphur Dioxide (SO2) emissions have been controlled by either dispersion or reduction. However worldwide environmental legislation now requires everyone to address SO2 emission, consequently regulations are in place in Indonesia to impose such controls on the operators of Coal Fired Power Plant. There are various methods to implement such reduction, and in coal fired power plant, the most common initial approach being to select, purchase and burn lower Sulphur fuel and frequently by the installation and operation of FGD systems. At Tanjung Jati B we burn low shulphur coals and apply a sea water, wet limestone FGD Process.
The FGD system at Tanjung Jati B principally comprices; limestone (reagent) offloading and handling system, limestone (reagent) preparations system, a dedicated Absorber area system, primary dewatering and chloride purge system, secondary dewatering system comprising two drum vacuum filter trains, and dedicated water systems.
Each unit combustion gas is directed to dedicated absorbers, where the gas passes through a slurry spray comprising the ground limestone and sea water. The absorber sump from where the slurry is recirculated is subject to forced aeration.
The simple FGD chemistry can be expressed :
SO2 + CaCO3 + 1/2H2O - CO2 + CaSO3.1/2H2O (Calcium Sulfite)
The oxidation process converts all of the liquid sulfite (and bisulfite) ions to sulfate ions, sulfate precipitates with calcium as gypsum CaSO3.1/2H2O + O2 + H2O - CaSO4.2H2O (Calcium sulfate/Gypsum). Water evaporates from the flue gas scrubbing liquid (sprays), as the flue gas cools to the adiabatic saturation temperature, consequently under equilibrium conditions, water must be added to the system to make up for water loss. If the scrubbing water was not bled from the system, the salts (chlorides) in the incoming make up water would gradually concentrate. Concequently chemistry and density (15% Suspended solids) is maintained by limestone slurry addition and slurry extraction in order to adjust pH.
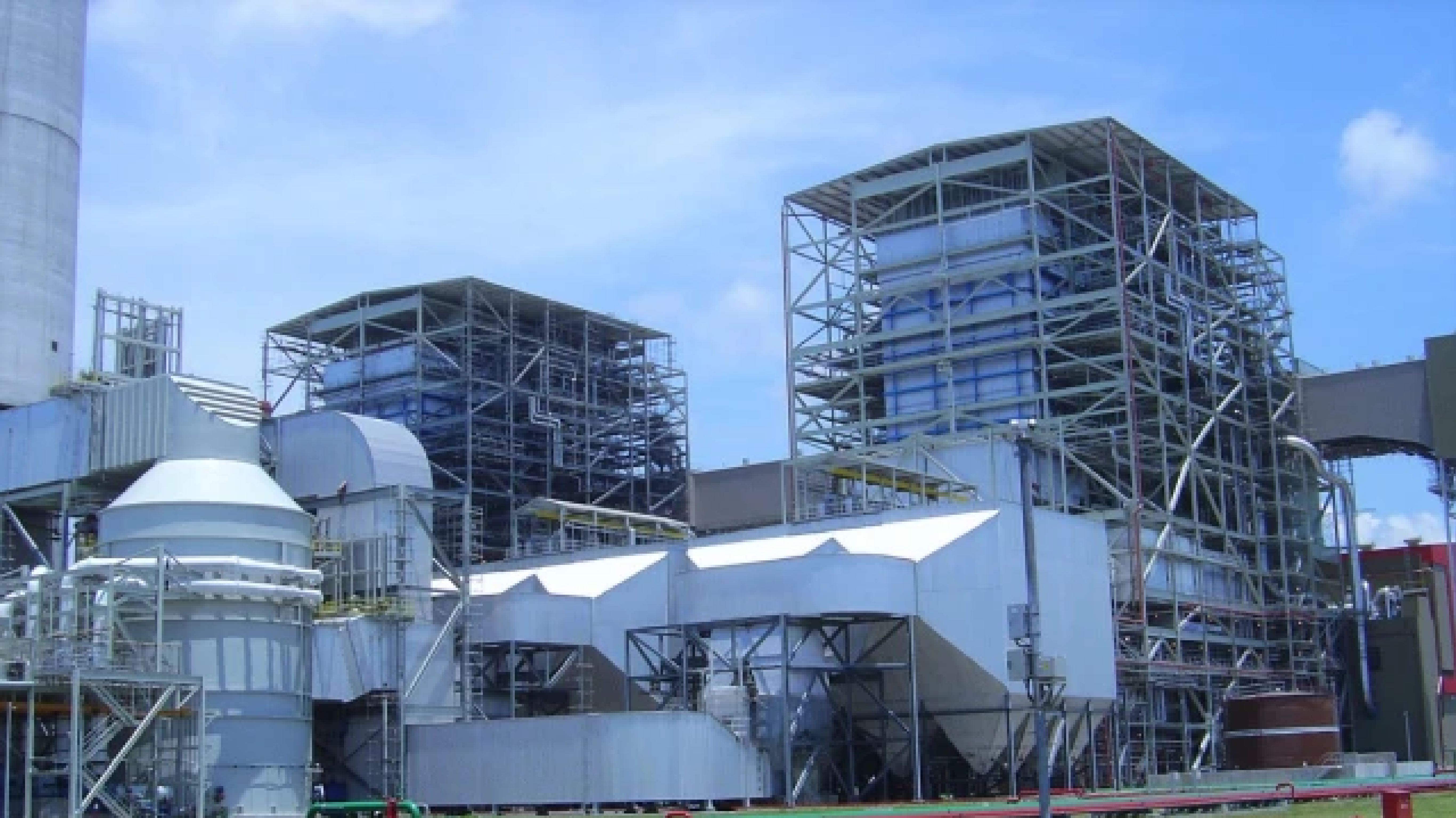
Bottom Ash Handling
The bottom ash handling system utilizes a Submerged Scraper Chain Conveyor (SSCC) beneath the furnace and submerged in the water seal. The conveyor continually discharges the bottom ash to a storage area adjacent to the boiler, from where it is loaded into ash transport trucks by front end loaders and transported to the ash storage area.
Fly Ash Handling Systems
In the vacuum fly ash convetance system ash is removed from each in units precipitator and economizer hoppers and transported by air to the fly ash silo's.
The fly ash silo's store and discharge the ash to trucks, utilizing pug mills as required. Fly ash is carefully loaded into the top of containment type tankers for final disposal to the ash storage area, or for collection and use by the Indonesian comment industry.
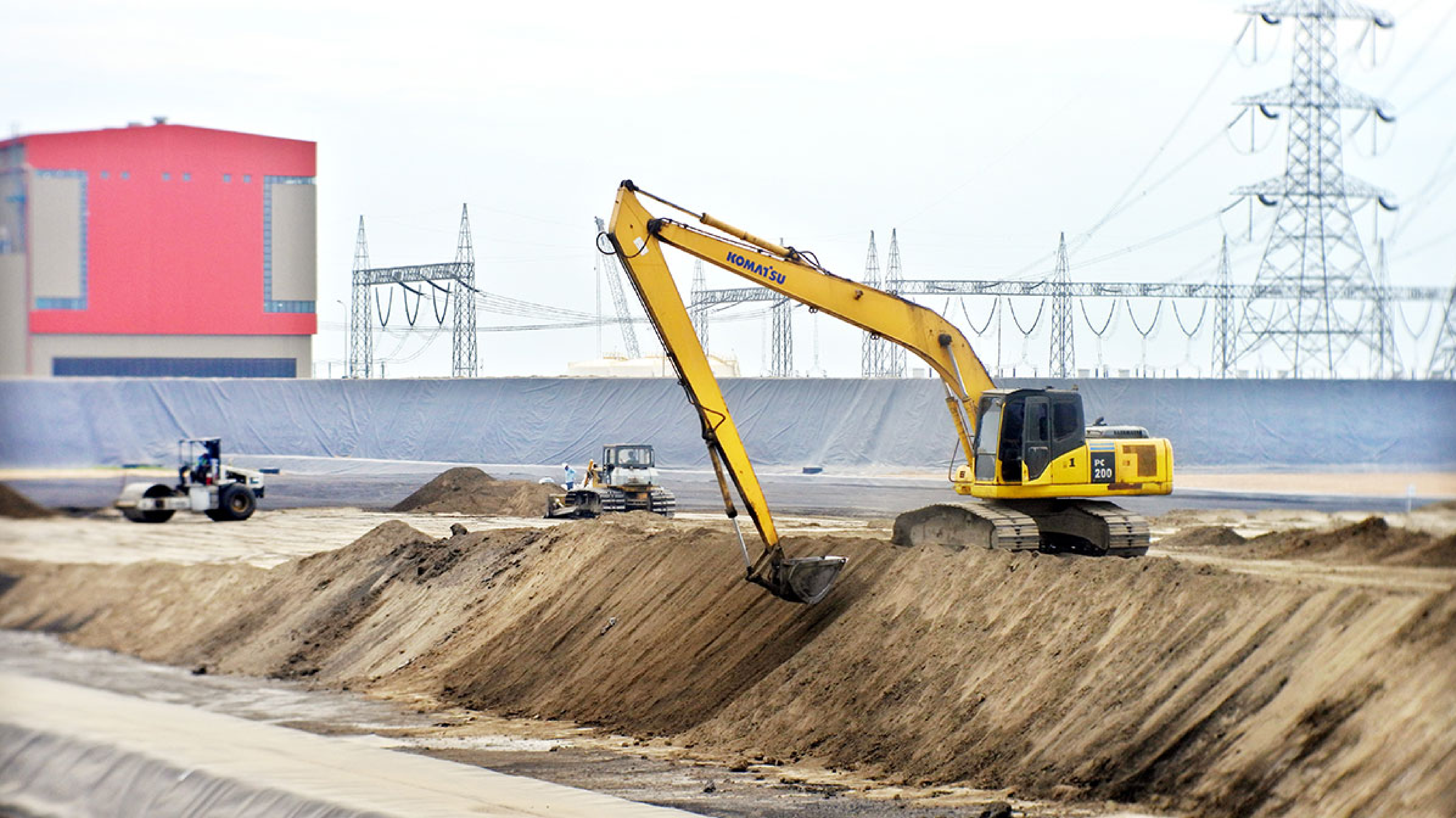
Plant waste water is minimal, however TJB has a waste water treatment plant to where all plant waste water is directed for treatment. The sources of the waste water include general plant waste water including Blowdown, coal plant run off, ash storage run off and other minor sources.
Waste water is collected in a retention basin, from where it is directed to a clarifier to remove suspended solids. The water is then moved to the neutralization basin where stable chemistry and pH adjustments are made before discharge. The process is designed to accommodate and adjust to maintain compliance with environmental regulatory requirements.
Comprehensive instrumentation is fitted to the plant to monitor the process, conditioning, and outflow. Should any monitored parameter indicate that it may be exceeding any measured parameter or water quality limits, the outflow is diverted to return to the retention basin for further processing.
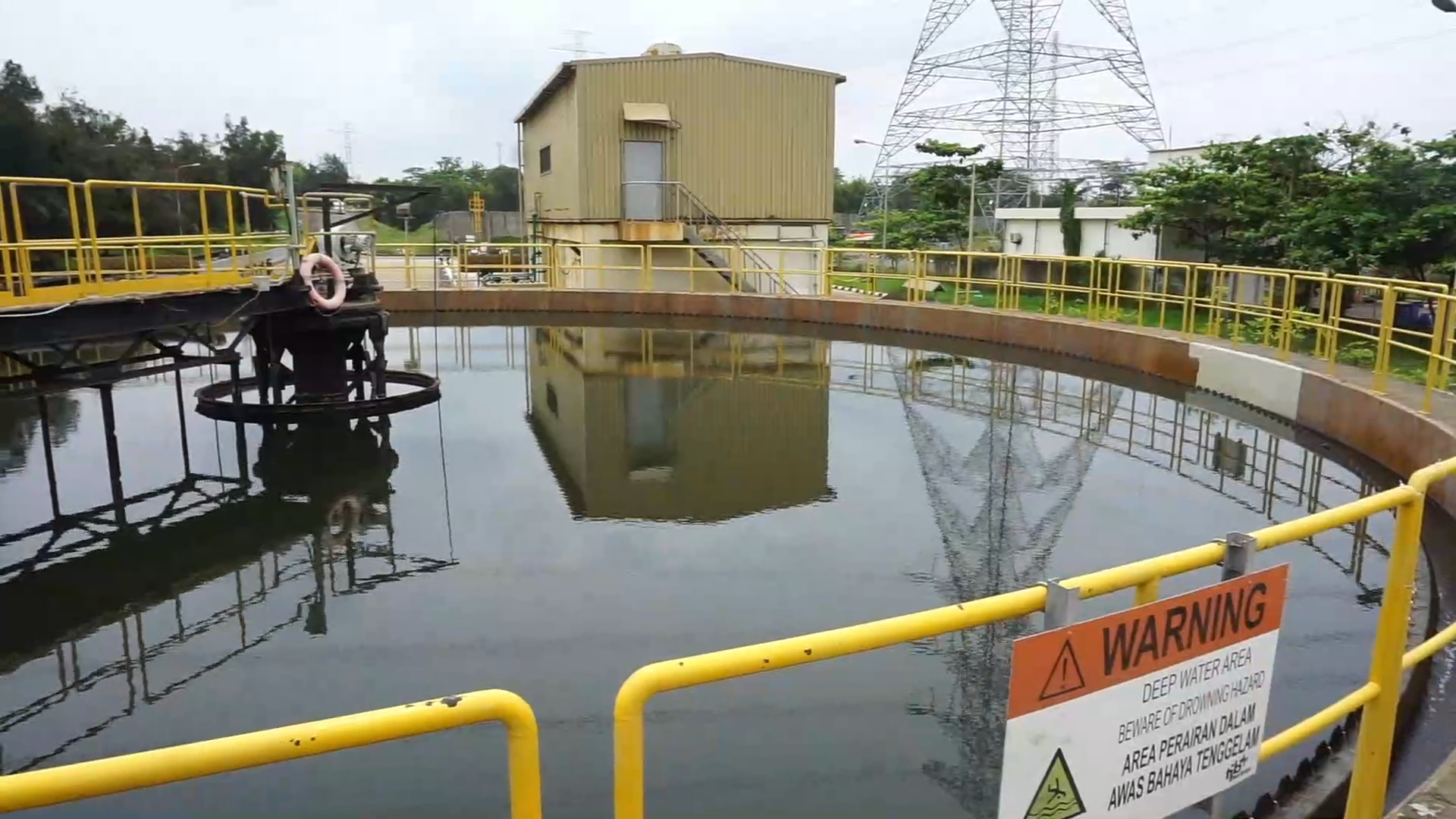